Our history
The story behind the success of Sendra Boots began over 100 years ago. More than 100 years that incorporate the expertise of four generations, from the brand's founder, Andrés Sendra, to his great-grandson Francisco Javier Sendra, present-day director of the company and leader of a truly great team of more than 170 specialists in boot fashion, design and manufacture.
What started out as a small family business has become one of the most important boot brands in the world, thanks to its expertise and capacity to keep on the move.
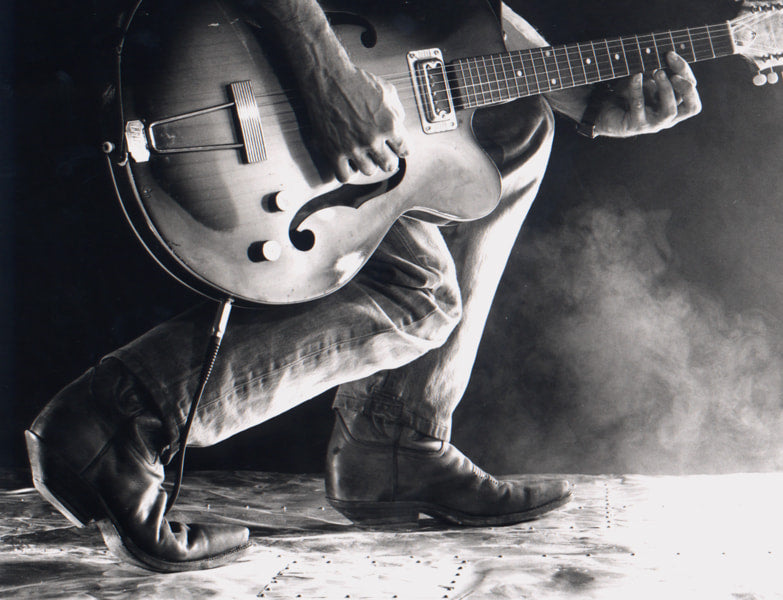
For Sendra, the 21st century is a time of continued development. After 100 years of existence dedicated to work and innovation, the curtain falls on its first century as the top boot manufacturing brand in Europe. Each year, 200,000 pairs of boots pass through the hands of 170 expert craftsmen in a process that includes 250 manufacturing operations.
The history behind Sendra − experts at setting traditions − and the solidity of its successful designs, created stitch by stitch, are together moulding its future one boot at a time. The passion and purposefulness of its team are paving the way to its continued success in the future.
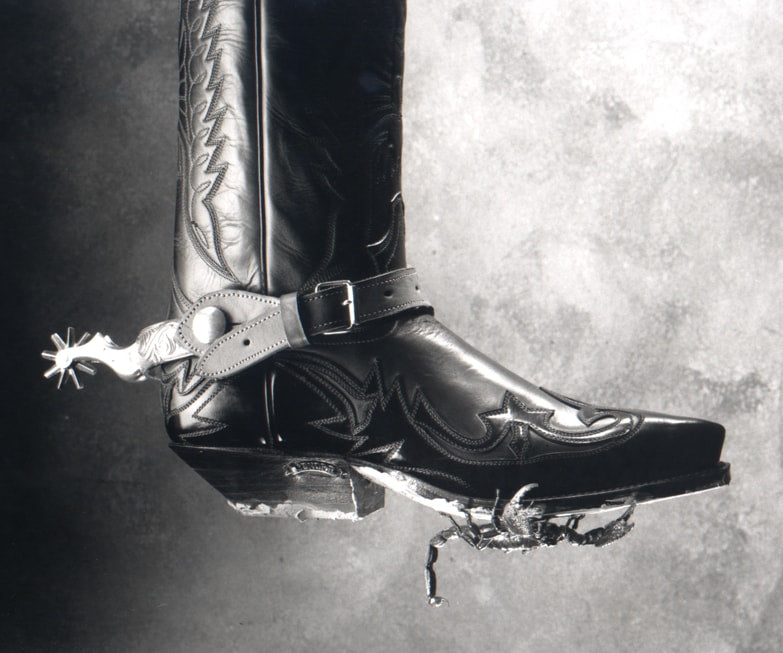
250 steps
Every morning, the factory comes to life and gives shape to the words of its Managing Director and designer, Javier Sendra. The hands of its craftsmen and its tireless machinery prepare to carefully mould the component parts into a true work of art.
Designing, cutting and shaping the leather, embroidering or piercing its signature motifs, putting together all its elements and giving each and every boot a perfect finish. These are the stages that make up Sendra's 250-step boot manufacturing process, key among which is Goodyear stitching − the technology underlying the Sendra brand’s reputation for unbeatable quality.
The Goodyear system involves double stitching the leather to the sole unit, making the boots very strong and long-lasting. The inner stitching joins the leather upper to the insole and the welt, while the outer stitching attaches the welt to the sole. The sole unit consists of two separate soles with a layer of cork between them to act as a thermal insulator and to optimize comfort by supporting the foot.
Next, the boot is lovingly sanded and polished around its edges and heels, before the dyes, Carnauba wax and aniline finishes are applied. The boot is then kept on the last for three days, time enough to ensure that the curves of the boot are set in the leather’s memory.
The route is precise, consistent and meticulous, with 250 production steps along the way, each one steeped in craftsmanship, care, quality and perfection.
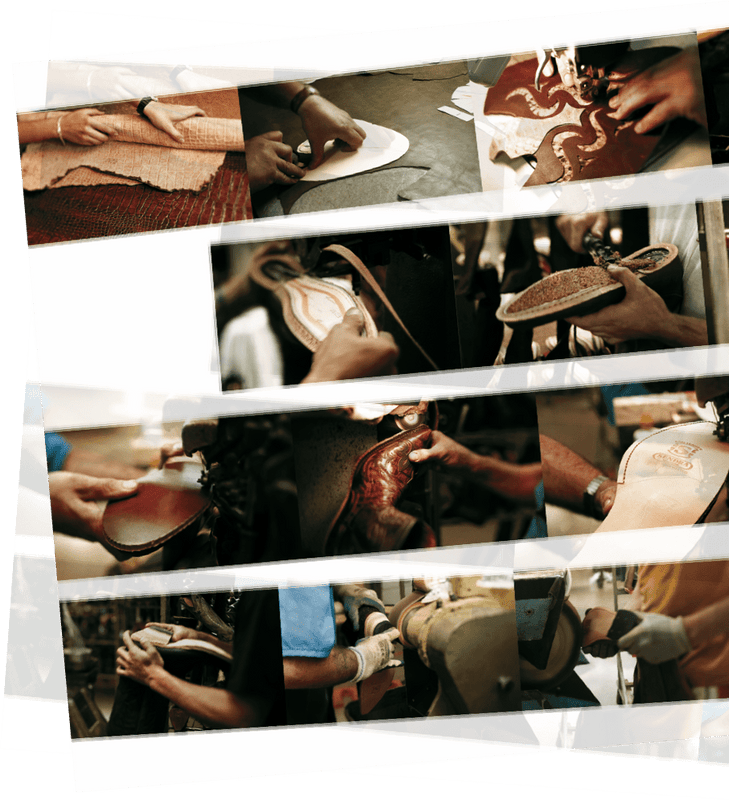